Case Study
SmartTechnic

Client
Industry
The Challenge
In 2019, whenPegasus Airlines, Turkiye’s second largest airline, wanted to digitise all functions of the airline operations daily maintenance process, which are traditionally managed using physical, paper logbooks, they contacted us.
The aim was to develop a fully mobile, digital platform, to improve performance efficiency and productivity within MRO processes and to be able to effectively track performance. Pegasus also required the continuous development of modules and features not present within their MRO system.
The completion of the maintenance process at the time of aircraft operation, with the simultaneous creation of the data in the MRO system, to be concurrently compatible with the operation, was of paramount importance.
Key Aims
- Ensure improvement in reporting, by standardizing defect and maintenance activity entries.
- Reduce manual errors.
- Increase data quality.
- Provide instant monitoring and measurement of maintenance processes (other than C Checks).
- Improve the employee experience.
- Increase safety.
- Improve on airline on time performance.
- Reduce costs.
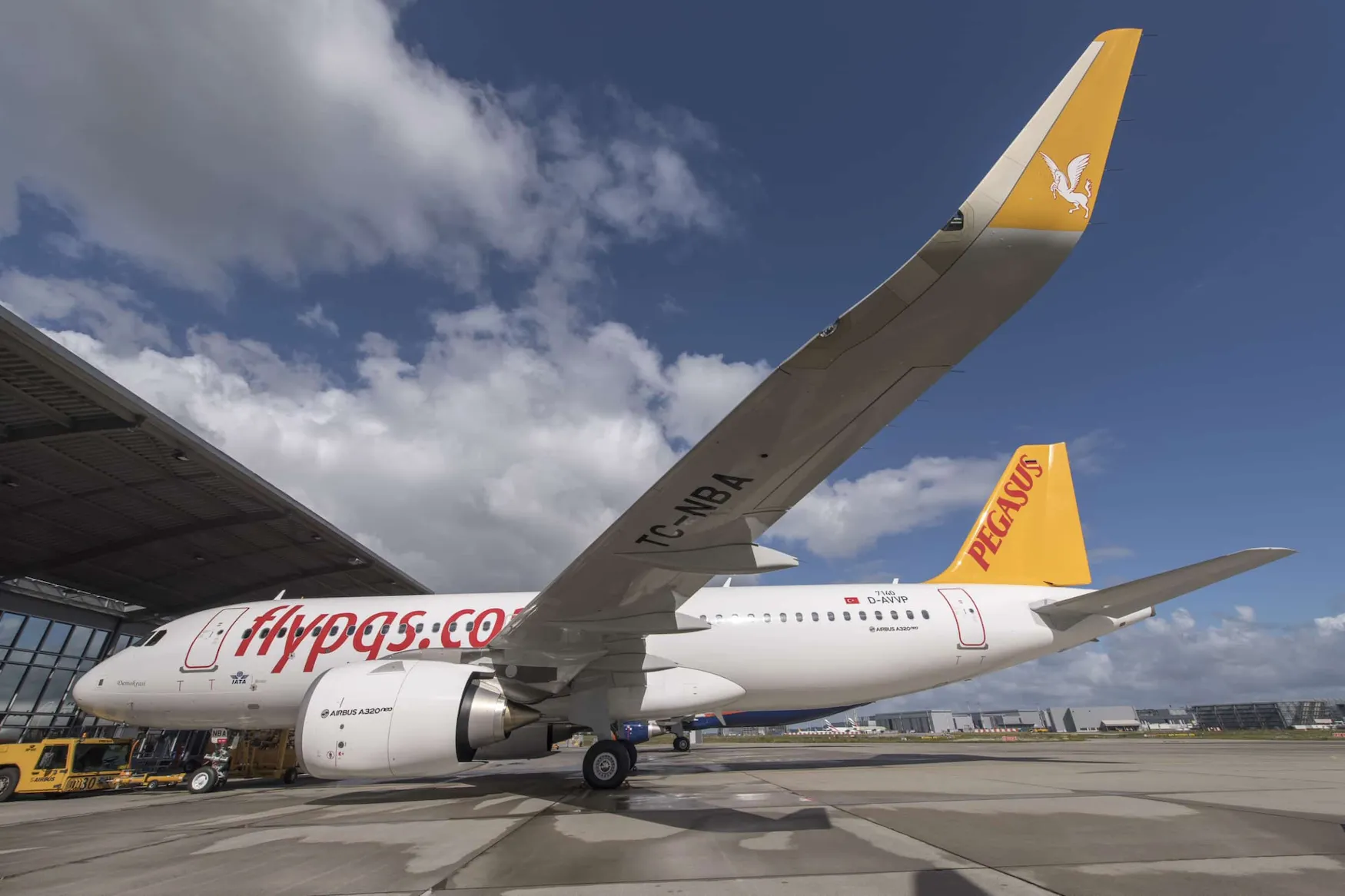
What We Developed
A completely digital airline ground operations platform that can be integrated with any airline MRO system and EFB Solution. Mobile applications were developed, natively, on iOS and Android to work on smart devices, to be used by cockpit and cabin crew as well as aircraft technicians.
A backend web application for use by System Administrators was also developed, to enable them to assign technicians to aircraft as well as define all related ground operations processes and definitions, including user roles and access privileges. The solution also provides shift leaders the opportunity to monitor aircraft maintenance activities in their shifts in real time.
After each aircraft maintenance activity, pdf documents digitally signed by the aircraft technicians, are recorded and stored as irrevocable. These documents are also always accessible.
Key Features
- Assign technicians to maintenance tasks.
- Location control.
- Open defects >>> Assign to technicians.
- Perform daily and pre-flight aircraft line checks.
- Perform historical fuel & oil uplift.
- Create flight logs.
- Defect creation with photo uploads.
- Defect diagnosis.
- Add maintenance action to defect, close and defer defect option.
- Store Maintenance Manuals.
- Make part requests.
- Make component changes.
- Pick slip, Tool Registration / Handover, Label booking completion.
- Dual / Duplicate Sign-Off.
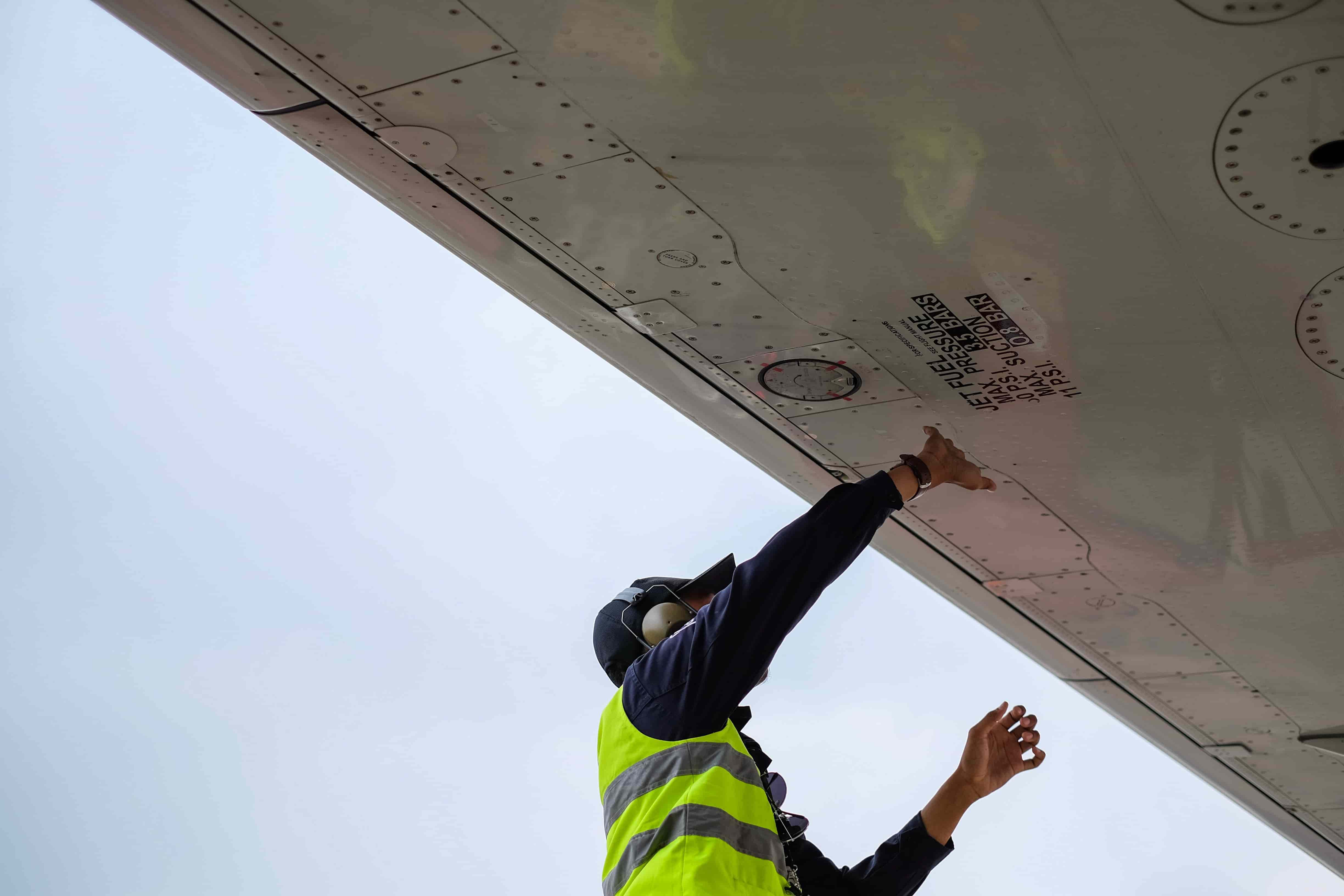
The results below reflect an accurate, high level indication of the benefits obtained and optimisations achieved within 12 months, as a direct result of the SmartTechnic paperless MRO solution being implemented by Pegasus Airlines.
Due to commercial confidentiality we are unable to provide exact figures here. However, we will be more than happy to put youı in touch with the respective teams at Pegasus Airlines or indeed arrange a site visit, if you'd like to request more information.
- 400+ Active users.
- 80,000+ successful transactions.
- Cost saving annually due to elimination of manual error.
- Eradication of logbook printing expenses.
- Reduction in archiving costs and man hours associated with the task.
- Improved on time performance due to reduction in technical delays.
- Significant cost optimisation annually.
Impact | Business Results
Crowned with a smooth changeover from a hardcopy technical log legacy system, SmartTechnic has enabled us to digitalize our line maintenance processes and achieve a major step to our fully-paperless goal. With the high project commitment and experience of Pinsoft, we believe we will establish a future-proof technology for all our inhouse maintenance processes, in line with our expectations; cost reduction and process optimisation.
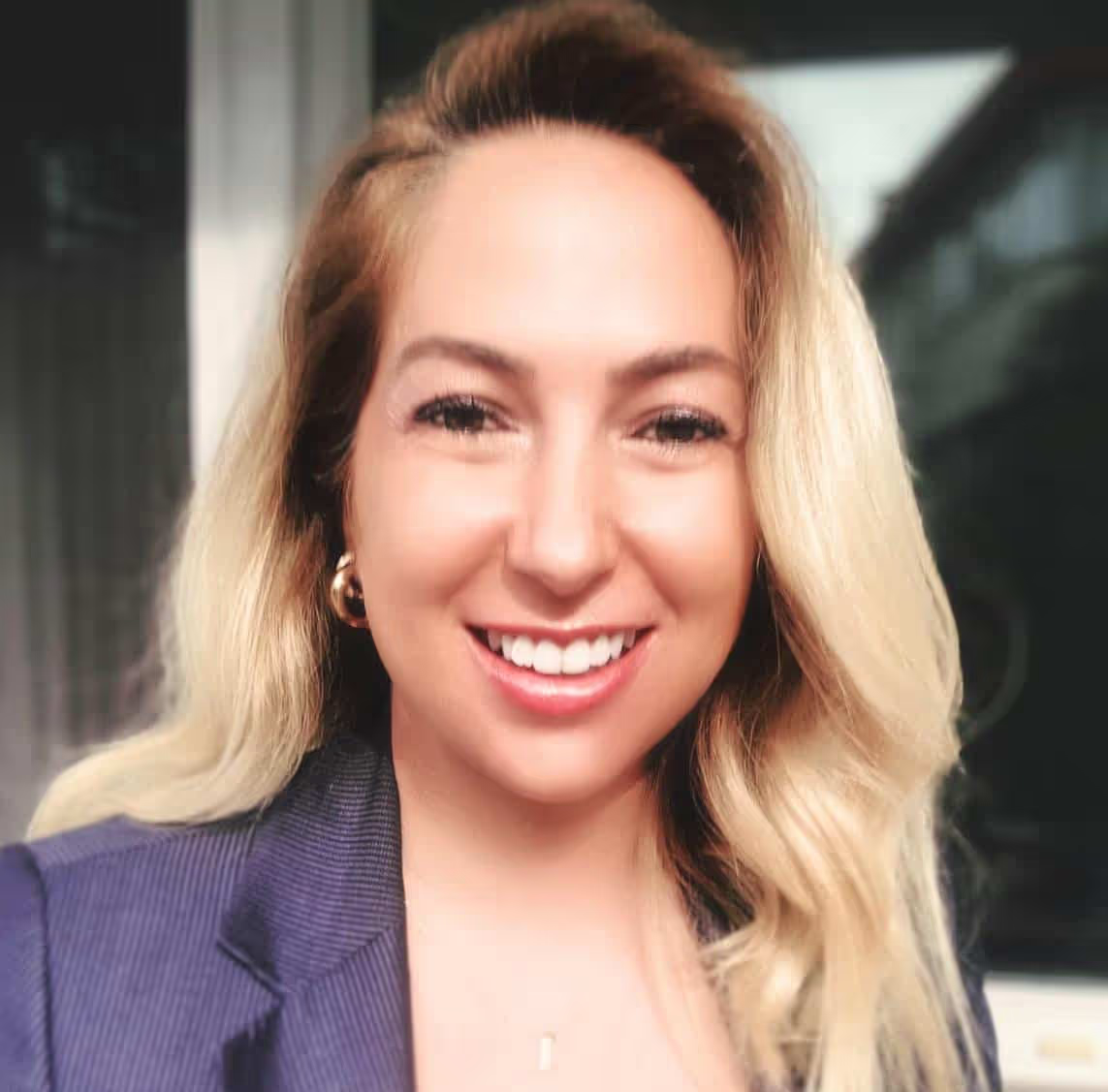